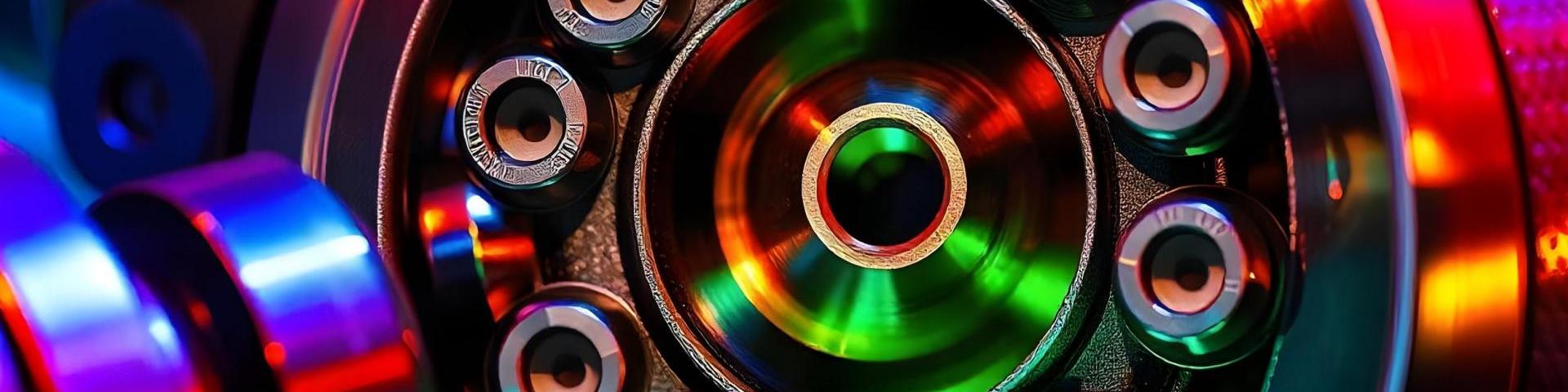
Everything You Need to Know About Plain Sliding Bearings: Applications, Materials, and more
What is a sliding bearing?
A sliding bearing is a mechanical component designed to reduce friction between two moving parts by providing a smooth surface for relative motion. Unlike rolling bearings, which use balls or rollers, sliding bearings rely on a lubricated surface for smooth operation. They are used in applications requiring stability, low maintenance, and high load-bearing capacity, such as motors, pumps, and heavy machinery.
What is a plain sliding bearing?
A plain sliding bearing, also known as a journal bearing, consists of a shaft and a bearing surface without any rolling elements like in ball bearings. The bearing works by maintaining a lubricating film between the shaft and bearing surface, minimizing direct contact and reducing friction. Plain sliding bearings are suitable for high-load, low-speed applications and are widely used in automotive, industrial, and marine machinery.
What materials are used in sliding bearings?
Sliding bearings are typically made from metals such as bronze, steel, or copper alloys, but composite materials, polymers, and ceramics are also used for specific applications. For instance, materials like PTFE (Teflon), aramid fibers, bronze are used for their low friction properties. Bearings made from these materials are designed to handle wear, corrosion, and high temperatures, making them suitable for heavy-duty and high-performance applications.
Why are plain sliding bearings important?
Plain sliding bearings play a crucial role in reducing friction, wear, and heat generation, ensuring smooth motion between parts. They are essential for supporting loads in machines and engines, such as in automotive and industrial equipment. Their simple design and cost-effective maintenance make them ideal for applications where high durability, high load-bearing capacity, and reliable performance are required, especially in harsh conditions.
How do sliding bearings differ from ball bearings?
Sliding bearings differ from ball bearings in that they rely on direct contact between the shaft and bearing surface, with a lubricating film to minimize friction. Ball bearings use rolling elements (balls) to reduce contact between surfaces, which allows for smoother motion and lower friction. Sliding bearings are often simpler, less expensive, and better suited for heavy-duty or low-speed applications, whereas ball bearings excel in high-speed and precision applications.
What industries use sliding bearings?
Sliding bearings are used in many industries, including automotive, aerospace, manufacturing, energy production, and heavy machinery. These industries require components that can handle high loads, reduce friction, and withstand harsh operating conditions. Sliding bearings are used in engine components, turbines, conveyors, suspension systems, and other high-stress machinery where smooth, efficient motion and durability are essential for performance and longevity.
How does Technymon contribute to sliding bearing technology?
Technymon manufactures advanced bearing materials, including composite bearings that offer superior performance, particularly in high-temperature and high-pressure applications. Their bearings are designed to provide low friction, reduce wear, and enhance operational efficiency. They also provide bearings that are resistant to corrosion, offer high load capacity, and are used in industries like automotive, aerospace, and energy, improving both durability and reliability.
What is the role of lubrication in sliding bearings?
Lubrication is essential in sliding bearings as it forms a thin film between the bearing surfaces, reducing direct contact and friction. This film helps to lower wear, minimize heat generation, and improve the efficiency of the bearing. Proper lubrication also prevents damage to the bearing material, extending its lifespan. The type of lubricant, whether oil, grease, or solid lubricants, depends on the operating environment and conditions of the bearing.
What is the benefit of composite sliding bearings?
Composite sliding bearings combine metal and polymer materials to offer enhanced wear resistance, reduced friction, and higher performance in demanding conditions. These bearings are particularly useful in high-load, high-speed, or high-temperature environments. They provide superior durability, corrosion resistance, and can handle more extreme conditions than traditional metal bearings. As a result, composite sliding bearings are increasingly used in industries such as automotive, aerospace, and industrial machinery for improved reliability.
How are Technymon sliding bearings designed for heavy-duty applications?
Technymon’ s sliding bearings are engineered to handle high-load, heavy-duty applications, using specialized materials and designs that optimize wear resistance and performance. These bearings are particularly suited for environments with high impact or high friction, such as automotive, construction machinery, and industrial equipment. Technymon incorporates advanced technologies like surface coatings and composite materials to extend the bearing’s lifespan, reduce maintenance costs, and ensure smooth operation in demanding conditions.
What is the advantage of using plain bearings in low-speed applications?
Plain bearings are ideal for low-speed applications because they provide smooth support for the moving parts without the complexity of rolling elements. They are cost-effective and simpler in design, which makes them easier to maintain. Since they rely on lubrication for smooth motion, they perform well in high-load conditions, where rolling bearings might face more wear. This makes them suitable for low-speed machinery like pumps, compressors, and engine components.
What is the expected lifespan of a sliding bearing?
The lifespan of a sliding bearing varies depending on factors like material, load, speed, and lubrication conditions. With proper maintenance, sliding bearings can last for many years. Regular inspections and adequate lubrication can help prevent wear and extend their service life. Bearings used in high-load or high-temperature environments might wear faster, but those made from advanced materials or composites are designed for enhanced durability and longer operational life in challenging conditions.
How does Technymon improve the performance of sliding bearings?
Technymon enhances the performance of sliding bearings by using advanced materials and coatings that offer improved wear resistance, reduced friction, and greater stability under extreme operating conditions. Their bearings are designed for high-performance applications in sectors like automotive, aerospace, and industrial machinery. By integrating materials like PTFE composites (MU, MR-5, ML-3) or bronze-based alloys (BRM, BMT) and aramid fiber-based material (Fritex, Fritex CRA), Technymon ensures that their bearings offer superior durability, high load capacity, and optimal functionality in harsh environments like high pressure or temperature.
What are the common applications of plain sliding bearings in automotive?
In automotive applications, plain sliding bearings are used in engine components, such as crankshafts, camshafts, and pistons, as well as in suspension systems, transmissions, and gearboxes. These bearings provide reliable support and reduce friction in parts that experience high stress and rotational motion. Their ability to handle high temperatures, reduce noise, and minimize wear makes them ideal for automotive engines, ensuring long-term durability and efficient performance in both standard and high-performance vehicles.
Can plain sliding bearings operate without lubrication?
Plain sliding bearings can technically operate without lubrication, but lubrication is highly recommended for optimal performance. Without lubrication, the bearing surfaces experience direct contact, which leads to increased friction, heat generation, and wear. Proper lubrication reduces these effects, extends the bearing’s lifespan, and ensures smooth operation. Some specialized plain bearings, such as self-lubricating bearings, are designed to function in situations where traditional lubrication may not be practical.
What is the difference between radial and axial sliding bearings?
Radial sliding bearings support loads that are perpendicular to the shaft axis, while axial sliding bearings handle loads parallel to the shaft axis. Radial bearings are often used in rotating machinery like motors and pumps, where the load acts outward from the shaft. Axial bearings are more common in applications such as thrust washers, where the load is directed along the axis of rotation. Both types reduce friction and wear in their respective applications.
What is the role of wear-resistant coatings in sliding bearings?
Wear-resistant coatings, such as PTFE or ceramic coatings, play a critical role in reducing friction and preventing material degradation in sliding bearings. These coatings create a smoother surface, which reduces direct contact between bearing surfaces and minimizes wear. They also enhance the bearing’s resistance to corrosion, heat, and environmental factors, allowing the bearings to perform better under harsh conditions. Coatings can extend bearing life and improve overall system efficiency.
How does temperature affect the performance of sliding bearings?
High temperatures can negatively impact the performance of sliding bearings by reducing the viscosity of lubricants, which leads to increased friction and wear. In extreme cases, it can cause bearing material to soften or deform. Temperature-resistant materials, such as those used by Technymon, are designed to withstand high temperatures while maintaining lubrication and performance. These materials ensure that bearings can operate efficiently even in industries like aerospace, automotive, and energy production, where heat is a factor.
What is the impact of load capacity on sliding bearing selection?
Selecting a sliding bearing with the correct load capacity is essential for ensuring long-term performance. Bearings that are subjected to loads beyond their capacity can experience increased friction, wear, or even failure. Bearings designed for high-load applications are made from stronger materials and feature enhanced wear resistance. Understanding the load conditions, including both static and dynamic loads, is crucial when choosing a sliding bearing to ensure it can handle the expected stresses without premature failure.
How can sliding bearings be maintained for optimal performance?
To maintain sliding bearings for optimal performance, regular lubrication is essential to minimize friction and wear. Bearings should be inspected periodically for signs of wear or damage, and contaminants like dirt should be removed. In environments with extreme temperatures or pressures, special maintenance procedures might be required, such as using high-performance lubricants or replacement of worn components. Following Technymon’ s recommendations ensure the longevity and efficiency of sliding bearings in any application.
What innovations does Technymon bring to the design of sliding bearings?
Technymon innovates the design of sliding bearings by incorporating advanced polymers and composite materials to improve wear resistance, reduce friction, and extend service life. Their bearings are specifically tailored for high-performance environments, including automotive and industrial machinery, where reliability under harsh conditions is critical. Technymon’ s use of self-lubricating materials further reduces maintenance needs, ensuring smooth operation and longevity even in extreme temperatures and pressures.
What is the importance of custom-designed sliding bearings for specialized applications for which Technymon is good in?
Custom-designed sliding bearings are essential for specialized applications where standard bearings may not meet the required performance criteria. By tailoring the design, material selection, and lubrication methods, Technymon can address unique operating conditions such as high temperatures, extreme pressures, or corrosive environments. Custom bearings offer enhanced reliability, longer life, and better efficiency in applications like aerospace, marine, and heavy industry, ensuring that the bearing performs optimally in demanding situations.
What technologies is Technymon developing to improve adhesion between different materials?
Technymon is developing advanced surface treatments and adhesive technologies that enhance the bond strength between diverse materials, such as metals, ceramics, and polymers. Their solutions often involve surface functionalization, where materials are treated at the molecular level to improve compatibility and adhesion. By using tailored adhesives and optimizing material interfaces, Technymon helps improve the durability and performance of composite materials in industries like automotive, aerospace, and energy.
What role does surface functionalization play in the adhesion of composite materials?
Surface functionalization involves altering the chemical composition of a material’s surface to create a more favorable bonding site for adhesives. Technymon employs functionalization techniques, such as grafting specific molecules or creating microstructure surfaces, to improve the interaction between different materials in a composite. This results in stronger and more reliable adhesion between dissimilar materials, such as metals and polymers, ensuring high performance and longevity in applications like construction, automotive, and industrial machinery.
How are different composite materials reinforced to form a single, stronger material?
To create a composite material from two or more different materials, Technymon combines materials with complementary properties to form a stronger, more durable material. For example, a polymer matrix might be reinforced with fibers like carbon or glass to improve strength, while ceramic materials can be incorporated for enhanced thermal resistance. Technymon uses advanced bonding agents and reinforcement techniques, such as resin infusion or hybrid composites, to bind these materials together, resulting in a cohesive, high-performance composite material.
What are the benefits of hybrid composite materials developed by Technymon?
Hybrid composite materials developed by Technymon combine two or more different types of reinforcing fibers, resins, or matrices to optimize the material properties. By integrating fibers like carbon, aramid, or glass with polymers or ceramics, these composites offer superior strength, flexibility, and thermal resistance. The combination ensures a balance of properties, making them ideal for high-performance applications such as aerospace, automotive, and energy, where both lightweight and durable materials are essential.