MX Pre-lubricated Bearings
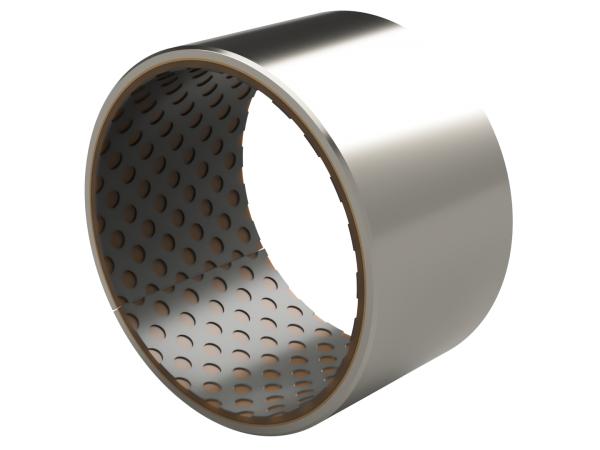
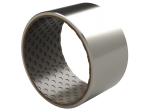
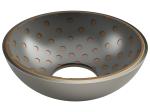
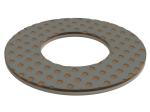
Multilayer bushing (Pre-Lubricated Sliding Bearings) MX bearings are Pre-lubricated material and are a three layer composite product.
A porous layer of bronze is sintered onto a steel backing. The purpose of this layer is to bond the upper acetal co-polymer sliding layer and to facilitate heat dissipation. The polymeric surface is indented so that the lubricating grease is collected and released gradually to minimize friction and protect the mating surface.
The MX range of products includes bushes, thrust washers and strips both in metric and imperial sizes. Furthermore, MX bearings can be supplied, on request, in metric or imperial sizes. MX is supplied in the pre-finished version, ready for use. X structure combines in the best way the mechanical strength of the steel, the bronze thermal
Operating Conditions
-
DRY -
OIL -
GREASE -
WATER -
PROCESS
FLUID
Please, fill this form for getting current Pricesheet and/or Drawings in DWG format. We will send you all files on your email.
All fields, which marked by an asterisk (*), are required.
Thank you for your interest in our company.
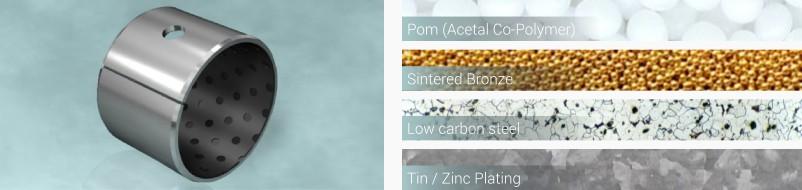
Structure of the material
Layer | Average analyses of the material | Thickness of layer |
---|---|---|
Sliding layer | Pom-C (DIN 7728) | 250 ÷ 450 μm (Average Peak) |
Intermediate layer | CuSn10 Sintered | 200 ÷ 350 μm (Average Peak) |
Connecting layer | Cu | 1 ÷ 3 μm |
Supporting shell | Low Carbon Steel (EN 10139)
|
0,50 ÷ 2,70 mm
|
Protective layer | Sn or Zn | 2 ÷ 8 μm |
Characteristics
MX structure combines in the best way the mechanical strength of the steel, the bronze thermal conductivity and POM-grease low friction. The performance are the following:
- Working surface acceptable specific static pressure max 140 N/mm2
- Working surface acceptable specific dynamic pressure max 70 N/mm2
- Maximum sliding speed with grease: 2,5 m/s (500fpm)
- Working temperature from: -40°C to +130°C (-40°F to +266°F)
MX is produced in coils of various thicknesses from which the sliding bearings such as bushes, thrust washers, strips and special parts for lubricated applications are manufactured. MX bearings can be used in a wide range of applications, from civil and industrial vehicles to machine tools and wherever there are articulated joints that require minimum periodic lubrication. The lubricant guarantees very low coefficients of friction and consequently, a reduced amount of wear with an anti-corrosive protection of the mechanical parts. Use of the MX bearings is continuing to expand because of a need both to overcome problems of wear between two metal mating surfaces and to reduce costs by substituting rolling bearings wherever possible. MX provides an answer to these requirements while offering greater compactness and ease of fitting at the same time. Lubrication is always necessary and if grease is used, it is essential to establish beforehand whether the grease will be applied only initially or if regular maintenance operations will be carried out. Further details concerning maintenance are provided further on. Apart from bushings and thrust washers the MX can be supplied as many other technical items,
Special Items
carried out. Further details concerning maintenance are provided further on. Apart from bushings and thrust washers the MX can be supplied as many other technical items, between them we indicate the followings:
- Bushings and washers at customer request measures
- Counter - roller bushings with the sliding surface on the outside diameter
- Special items at customer’s drawing.
Performance
The load capacity of MX bearings is expressed by the load factor p x v (N/mm2 x m/s) where p is the specific load and v is the speed. The maximum value of the specific load that can be applied under static and ideal conditions is 140 x N/mm2. For the bushes, the internal semi-surface, which is given by the result of the internal diameter multiplied by the length Di x L, must be considered. The value of the specific load is reduced to 70 N/mm2 under dynamic conditions ( with grease lubrication)
Higher temperatures reduce the load factor by 20% at 50°C, by 50% at 70°C and by 80% at 100°C. The performance of the bearings in the MX range is improved with grease lubrication that allows for P x V factors of up to 5 (N/mm2 x m/s) with maximum speed of 2.5 m/s. The MX series of bearings can be used without maintenance and with just a first initial greasing. However, where possible, re-greasing should be carried out to increase the operating life of the bearing.
The outside of the bearings is protected with a Tin Plating or Zinc Plating.
Friction
The particular characteristic of the acetal co-polymer sliding lining of MX bearings is that it creates a pseudo-binding with the lubricants to form an excellent and very long-lasting sliding surface. Apart from the considerations referred to above, the dynamic coefficient of friction under lubricated operating conditions is greatly influenced, both positively and negatively, by the same factors that determine the operating life of the bearing. With a grease based lubrication, the coefficient of friction varies between the values of 0.05 - 0.12. The lowest values are reached with a high specific load. Oil lubrication further reduces friction and at high speeds hydrodynamic lubrication is attained that lowers the coefficient of friction to values close to 0,02. For MX bearings, the static coefficient of friction is not much higher than the dynamic one and therefore, the annoying “stick-slip” phenomenon, i.e. the sticking of the bearing when still, does not occur.
Wear
The wear rate of MX bearings for greased applications is difficult to calculate in advance owing to other factors that must be taken into consideration apart from the temperature, such as the roughness of the mating surface, the alignment of the mating, the presence of pollutants in the lubricant and other elements.
The operating life is also affected by the way in which the load is applied. With an equal specific load, the operating life is longer if the application has a rotating load, while it is shorter (-30% approximately) with a unidirectional load, while thrust washers have the shortest operating life (-50% approximately).
The amount of wear on MX bearings is very small especially for specific loads from 10 to 20 N/mm2. Even for loads of up to 120 N/mm2, the amount of wear remains low as long as the lubricant is well-distributed, but the amount of wear increases enormously as soon as the lubricant runs dry. The bearing must be regreased before wear begins due to a lack of lubricant and, generally, the amount of wear between one lubrication and the next should not exceed 0,025 mm. When the amount of wear reaches 0,15 mm., the bearing is normally considered to have exceeded its operating life
Mounting
Base procedure for bushings mounting is to force them into their seats; there are same suggestion to follow:
- Machine a 1 mm seat lead - in with an angle of 20° (±5°)
- Clean and burr the pieces to couple
- Lubricate external bushing surface before mounting
- Check alignment between seat and bushing centre lines
- When 2 bushing are needed their junctions must be aligned
- Use a proper sized mandrel when possible.
- Mounting can be done with hydraulic or mechanical tools.
The mounting force (F) in Newton is shown in the attached table.
Bushing Nominal Thickness 0,50 ÷ 1,00 mm | F = 300 x L (Length of bush) |
Bushing Nominal Thickness 1,00 ÷ 1,50 mm | F = 500 x L (Length of bush) |
Bushing Nominal Thickness 1,50 ÷ 2,00 mm | F = 700 x L (Length of bush) |
Bushing Nominal Thickness 2,00 ÷ 2,50 mm | F = 900 x L (Length of bush) |
When mounting larger bushes it is advisable to use a mounting tool to support the bush. The tool diameter should be 0,3 ÷ 0,4 mm more than the bush diameter. If the bush is secured by using an adhesive, care must be taken to ensure that good quality adhesive are used and that it does not get onto the sliding surface.