TWM Self-Lubricated Bearings
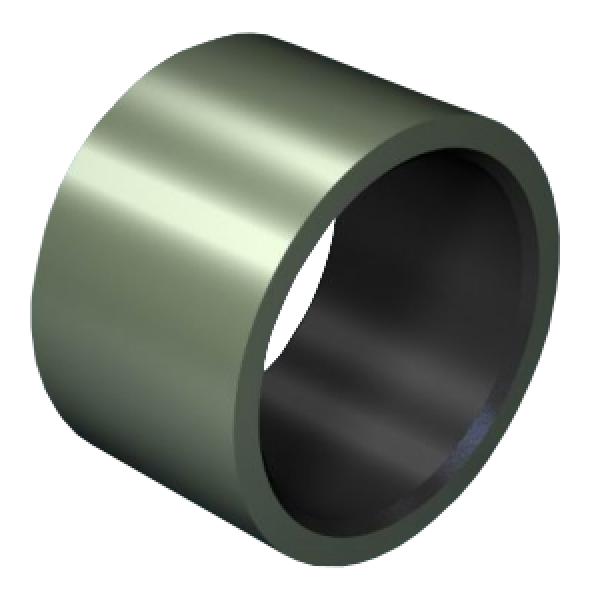
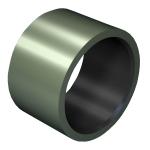
TWM identifies an entire sliding bearing family constituted from a complex fibre-winding technique. The highstrength backing consists of glass fibres and the sliding surface is made of PTFE and polymer fibres. Both layers are embedded in an epoxy resin matrix. This material selection combines the special mechanical properties of glass fibres with the outstanding tribological properties of PTFE and the high-strength polymer fibres.
Operating Conditions
-
DRY -
OIL -
GREASE -
WATER -
PROCESS
FLUID
Please, fill this form for getting current Pricesheet and/or Drawings in DWG format. We will send you all files on your email.
All fields, which marked by an asterisk (*), are required.
Thank you for your interest in our company.
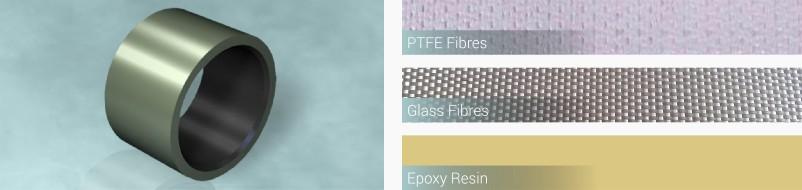
Characteristics
TWM benefits are for extreme operating conditions, most plain bearings need premature maintenance or replacement, TWM bushing are typically still operational.
- Excellent sliding property;
- High load carrying capacity;
- Long service life;
- Maintenance-free;
- Insensitivity to edge loading and misalignment;
- Good impact resistance;
- Good noise and vibration damping;
- Excellent resistance to corrosive media, even to salt water, and many chemicals;
- Good insulator preventing passage of eletric current;
Properties
Maximum Specific Load Static | 230 N/mm2 (33350 psi) |
Maximum Specific Load Dynamic | 125 N/mm2 (18130 psi) |
Maximum PxV Factor | 1,05 N/mm2*m/s |
Maximum PxV Factor short period | 1,50 N/mm2*m/s |
Maximum Sliding Speed Dry | 0,10 m/s (20 fpm) |
Break Straw | 350 N/mm2 |
Max Moisture Absorption (23°C) | 0,2% (ASTM D570) |
Service Temperature Maximum | +140°C (+284°F) |
Service Temperature Minimum | -100°C (-148°F) |
Shaft Finish Ra (Advised) | 0,2÷0,8 Ra μm |
Shaft Hardness (Advised) | >350 HB |
Dimensions
The dimensions of TWM bushing correspond to ISO 4379 (1993). This provides full interchangeability with other bushings, e.g. bronze bushings. The tolerances after fitting into housing bore with H7 tolerance, will be within D11.
Mounting
Base procedure for bushings mounting is to force them into their seats; there are same suggestion to follow:
- Machine a 1 mm seat lead - in with an angle of 20° (±5°)
- Check alignment between seat and bushing centre lines
- Use a proper sized mandrel when possible.
- Mounting can be done with hydraulic or mechanical tools.
- We suggest to lubricate the internal surface just in start-up fazes.