BMT Pre-lubricated Bearings
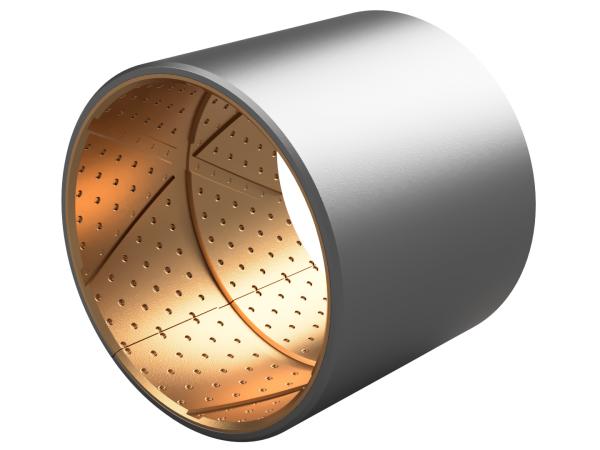
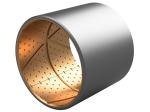
BMT identifies an entire sliding bearing family constituted from a low carbon steel support over lined by a second layer of thermally sintered bronze. The lubricated bronze surface is the sliding side of the bearings. With oil or grease lubrication these bearings are ideal for all the applications where high strength, minimum dimensions and low friction factor are required. This material is produced in according to ISO 3547-4 Key S6 Designation CuPb10Sn10. The sintered layer is generally of lead bronze (CuSnPb10) which is ideal for sliding couplings with steel. Standard bronze thickness is 0,30 mm (nominal) which may be increased to 0,40 mm (nominal) and more for extra thickness bearings (BMT-4 bearing line).
Operating Conditions
-
DRY -
OIL -
GREASE -
WATER -
PROCESS
FLUID
Please, fill this form for getting current Pricesheet and/or Drawings in DWG format. We will send you all files on your email.
All fields, which marked by an asterisk (*), are required.
Thank you for your interest in our company.
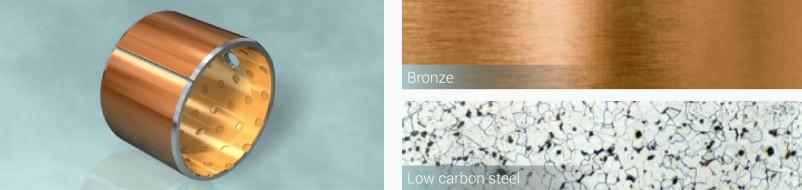
Structure of the material
Layer | Average analyses of the material | Thickness of layer |
---|---|---|
Sliding layer | Sinter Bronze (UNI ISO 4383)
|
200 ÷ 350 m Std.
|
Connecting layer | Cu | 1 ÷ 3 μ |
Supporting shell | DC 04 (EN 10139)
|
0,5 ÷ 2,70 mm
|
External Protective layer | Cu | 1 ÷ 3 μ
|
Characteristics
The BMT sliding bearings family is broken down into four product lines which differ from the finishing and from the thickness of the bronze layer; the identifications are the following:
BMT-1 = sliding surface with spherical cup lubricant pockets dedicated to applications without constant lubrication, the surface pockets accumulate and progressively release the lubricant.
BMT-3 = plain bronze surface to be applied where constant lubrication is foreseen, in this sense, according to customer specification, the bronze surface can be stamped or machined to obtain lubricant channels.
BMT-4 = plain surface with 0,10÷0,15 mm extra nominal thickness of bronze layer, it has an increased bronze thickness which is requested for all the applications with "in seat" final machining; typical case is the "in seat" machining of bushings for close tolerance alignment.
Main items for all the BMT range are the cylindrical bushings ISO 3547 (DIN 1494) and the flanged cylindrical bushings, metric and imperial; there are also thrust washers, support strips and a wide range of special items to customer drawings.
BMT sliding bearings offer many advantages, including the following :
- easy installation and maintenance
- high load capacity
- very compact dimensions
- high thermal conductibility
- wide range of working temperature
- wide availability of standard bushings
- possibility for special items
Sliding Surface
BMT sliding bearings must always be used with lubrication. For the applications where the lubrication can only be periodic grease must be adopted. Where the lubrication can be continuous a lubricant oil can be chosen. The lubricant pockets and channel grooves reduce the working surface so the loading capabilities of the BMT bearings. Top performances are obtained with BMT-3 and BMT-4 having plain surface; with these it is possible to reach the hydrodynamic running at high load factor (Speed x Load).
The presence of the pockets reduces the working surfaces by the following percentages:
- BMT-1 SPHERICAL CAP POCKETS 21% reduction
- BMT-3 & 4 the reduction, with channel grooves, must be calculated case by case.
- BMT-1 with the spherical pockets ensure an optimum lubricant release and it can be used with oil and grease.
We can offer BMT bushings and all other sliding bearing types with different lubricant pockets and channel grooves according to customer drawing.
Design Data
To choose the right BRM-10/80 sliding bearing one must know the maximum applicable load, the sliding speed, the type and the intensity of the lubrication, the hardness and the roughness of the counter piece surface; after that the mechanical characteristics to consider are listed here below.
Hardness HB 2,5/ 62,5/10 | 110-140 |
---|---|
Roughness Ra | <0,5 μm |
Thermal conductibility | 60 W/m.K |
Coefficient of thermal expansion | 20 x 10-5/°C |
Coefficient of friction (with oil or grease) | 0.06 ÷ 0.17 |
Service Temperature | -40°C to 150°C (-40°F to 300°F) |
Maximum Speed (with oil or grease) | 2.5 m/s (500 fpm) |
Maximum PV factor (with oil or grease) | 2.7 N/mm2 * m/s |
Maximum work load Static | 150 N/mm2 |
Maximum work load Dynamic | 60 N/mm2 |
Lubrication
Lubrication is strictly needed for the correct use of BRM-10/80 sliding bearings; lubrication is also useful to prevent corrosion on the counter pieces. When the coupling is exposed to atmosphere or to aggressive environments it's advisable to adopt lubricant seals which always improve coupling service life.
Mounting
Base procedure for bushings mounting is to force them into their seats; there are some suggestion to follow:
- Machine a 1 mm seat lead - in with an angle of 20° (±5°)
- Clean and burr the pieces to couple
- Lubricate external bushing surface before mounting
- Check alignment between seat and bushing centre lines
- When 2 bushing are needed their junctions must be aligned
- Use a proper sized mandrel when possible.
- Mounting can be done with hydraulic or mechanical tools.
The mounting force (F) in Newton is shown in the attached table.
Bushing Nominal Thickness 0,50 ÷ 1,00 mm | F = 300 x L (Length of bush) |
Bushing Nominal Thickness 1,00 ÷ 1,50 mm | F = 500 x L (Length of bush) |
Bushing Nominal Thickness 1,50 ÷ 2,00 mm | F = 700 x L (Length of bush) |
Bushing Nominal Thickness 2,00 ÷ 2,50 mm | F = 900 x L (Length of bush) |
When mounting larger bushes it is advisable to use a mounting tool to support the bush. The tool diameter should be 0,3 ÷ 0,4 mm more than the bush diameter. If the bush is secured by using an adhesive, care must be taken to ensure that good quality adhesive are used and that it does not get onto the sliding surface.